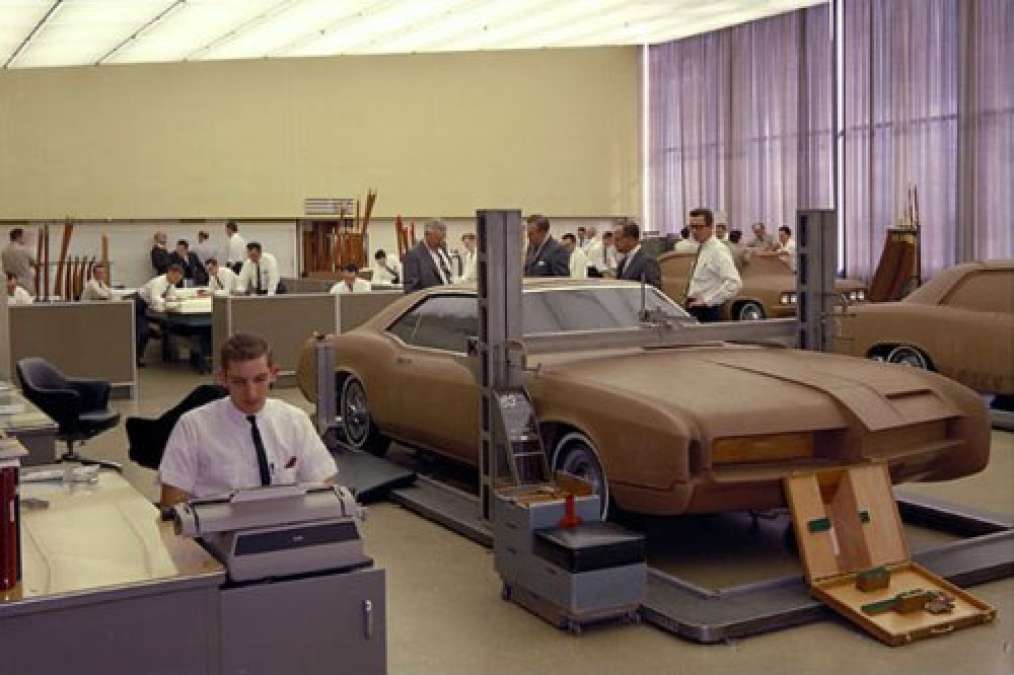
Starting with nothing more than an idea sketched on paper, the process of taking a car to a gleaming production concept on the auto show floor typically takes about three years. At any point along that path, the design can be fundamentally changed or even thrown out. Designers quickly learn that their idea is not necessarily going to become reality most of the time.
Three years is not set in stone - some designs take longer while others can often shortcut and take less time. In general, though, there are several steps for a design to go through before becoming a showroom-ready vehicle.
Drawing / rendering is the first step. This usually begins with a simple sketch or series of sketches by a single designer with an idea. In movies, television, and marketing materials for new designs, this is usually the focus of things - the most "glamorous." The designer's sketch can come from anywhere - a personal idea submitted to a design lead, a call for designs from company-wide studios, or even (rarely) freelance designers bringing an idea to the company for consideration. Thousands of designs are often submitted to an auto manufacturer every year and only one or two of those may eventually see showroom floors.
Packaging is the first modification. The initial design concept is then put through changes as packaging considerations (engine availability, drive train layouts, and other safety requirements) are made. This is where most of the fundamental changes to the design will take place. For the artist who created the vehicle to start with, this is generally where art meets reality and compromises are made. At this point, the car is still on paper, but will undergo several changes and re-drawings until general engineering needs are met.
Computer and clay modeling comes next, as 2-D renderings become 3-D reality. At this point, the two-dimensional drawings on paper are converted to three dimensions. This begins with computer renderings used not only to visualize the concept as an object, but also to see the car's physical dimensions in measured terms so that detailed drafts can be drawn. Those drafts are then used to create a physical, clay model - usually by hand. Modern contrivances, such as 3-D printers, are slowly eking their way into this process, but only very slowly and usually alongside rather than replacing traditional clay modeling.
Quite often, during this modeling process, multiple versions of the design concept are being considered and so more than one clay model may be produced. It's actually unusual at this point for a clay model to be full-sized, they are usually scaled to be smaller than full size to save time. A full-sized clay model will not be done unless only one design is chosen and designers or engineers need a full rendering.
Full modeling then takes place with the chosen design. This full model can be of clay, but may also be made of polymers or combinations of materials other than clay to make a lighter, more easily transported model. Clay is still the industry standard, but is seeing replacement by other options as they become cheaper and easier to work with. This full-sized model, once finished, will look like a real car and is often photographed and used as initial marketing material.
Interior sketching and modeling then begins. The interior has often already been sketched by the original designer for the vehicle. Like the exterior, however, it will have gone through several re-designs and drawings as a sub-team of the overall design team re-considers the interior's look and dimensions to fit with the overall changes that have been made to the car thus far. Sketches become computer renderings, which become CAD drawings, and then become clay models - usually three or four - to show options available. The look and feel of everything from the steering wheel to the seating and control surfaces will be gone over in detail here.
Colors, materials, etc. are now chosen. Once final design choices are made for both exterior and interior, designers then begin going through the hundreds (even thousands) of options available to them for paint, trim colors, fabrics, plastics, accessories, etc. Often, new things will be available thanks to the company's teams of hunter-gatherers who're continually scouring the globe for new options and ideas for everything from fabrics to industrial materials.
Dashboard and driver control elements are chosen. Along with the trim and color choices, detailed models of the interior are also used to make adjustments and refinements to the driver's controls and the dashboard's displays and design. Ergonomic changes are usually finalized at this point using real-to-life models made of plastic or clay. Many of these choices include marketing analysis.
Testing and refinement of materials is next. Final choices aren't quite final yet, since they have to withstand time and use tests to ensure that they won't be brittle or show color fade too quickly. Many of the elements will have already been subjected to these tests, but new options or materials will require testing for various environmental stresses. Heat and cold, direct sunlight, hands-on use, etc. will show whether the material can withstand everyday use. These tests are done in laboratories with real-to-life models made from the materials in question. They will be put under heat lamps, rubbed incessantly with robotic "hands", thumped with robotic arms to simulate human use, rained and snowed on, heated and cooled in ever-increasing intensities, etc. When proven, they will be OK'd, but if they fail, another option will be found.
Final modeling now takes place as the interior and exterior are combined. Outside of the computer, up to this point, the car has never been in one piece. Designers and engineers can now look at a physical model of the car in its full form, interior and exterior. This is often referred to as the "concept" phase for marketing, as it is now a physical reality. This is when engineering considerations for production begin to play heavily into the finalized, production design.
Model approval given. Management and (possibly) the company's Board of Directors will now give final approval for the vehicle. Marketing is often heavily involved at this point. If the vehicle is to be built, it will be given final approval now. Often, concepts never become more than just a concept, but are used for marketing purposes and will move forward anyway. Often, several concept models will be built (all by hand) out of the materials planned for use so that they can be showcased at auto shows and events. Some will be "sleds" with no working drive train present while others will be drive-able, working vehicles.
Final engineering and production concept completed, production begins. Engineers who specialize in the tooling of factories and building of vehicles will make final adjustments to the vehicle's design in order to make it enter production faster and cost less money to produce. These changes often involve details in how individual parts are put together, which parts will be used (sourcing), and so on. The final production process for the vehicle will be laid out and planned in real terms so that the phases of construction, from bare frame to finished car, are mapped and the factory tooling required for it are engineered. Other details such as spec sheets and information for factory workers on the line, vehicle testing requirements once initial models are produced, etc. are hammered out.
During the process, the original concept and the final production model are often very different vehicles. The dreaminess of paper drawings has solidified into the reality of a functioning automobile ready for consumers. The process has been completed in as little as a year for re-designs of existing vehicles to decades for some new, very advanced concepts. Most designs take 3-5 years to go from initial concept to consumer-ready production units.
Most manufacturers have models on a 4-6 year "remodel circuit" which means they will undergo a major remodeling in look and powertrain every 4 to 6 years. Variances are often made depending on sales figures, segment market changes, and marketing plans.
Comments
Informative artice. I would
Permalink
Informative artice. I would tend to modify that first step, though. Fact is, a marketing survey along with a business case is what really starts the design process. Think about it; without knowing the market and the vehicle size, the sketch might miss the mark. Is it a four door, two door, SUV, sport coupe, family sedan? In addition, that information sets up the next big question: Do you design a new architectue? Or do you modify an existing one to save tooling cost?
Regardless, a group called vehical architecture establishes the platform layout so as to give dimension to the plan, like wheelbase, steering column angle, sight lines, etc. Then and only then do the sketches come to fruition with any meaning.
One area that has definitely changed, though, are the CNC machines in the studios that literally mill the clay from the works derived from digiital sculptors. Any work on the clay after that is merely cosmetic scraping and filling in the low spots..
And speaking of cosmetics and details, stereo-lithography (SLA) parts are designed by those same digital sculptors, later formed/molded, painted and placed onto the clay, such as centerstacks, radios, controls, knobs, etc. This technology provides a greater 3D look and feel to the studio product so management can better make decisions. Even then they can argue over changing a silly millimeter.
In addition, the use of laser scanning technology which allows the clay to be digitized back into the CAD system, allows the engineers to work with 3D data as opposed to drafting sections that are limited in scope.
Another important entry is the greater use of studio engineers who now create zones and limit models as criteria so as to guide the digital sculptors, thus eliminating wasteful time redoing models. This makes engineering part of the design process. That pretty much described my world and job.
I miss the work at times but not the constant pressure, deadlines and incessant whining over criteria that the designers always feel limits their creativity, forgetting that new designs have a cost associated with them.
Thanks, Frank. I kind of
Permalink
In reply to Informative artice. I would by Frank Sherosky
Thanks, Frank. I kind of assumed that the segment would already be known for step 1, I guess. I spoke with three different designers for two different manufacturers over the past few weeks in odds-and-ends conversations and eventually got the idea to write this. Had I known you had done this for a living, I would have talked to you too. :)
I have a concept design for
Permalink
I have a concept design for GM that would blow the sales completely out of the water bringing back an old favorite. My problem is I don't know how to submit it to General Motors for review.
Robert, I am from South
Permalink
In reply to I have a concept design for by Robert Terry (not verified)
Robert, I am from South Africa where GM left the car market completely. So, we want to explore the market left by GM's Chevrolet marquee. I wrote to GM to assist us in closing this gap, but they declined our request. Perhaps, we can communicate with you regarding the concept design you have, and see how can we work it out.
South Africa does not have a car manufacturer, but there are developmental steps taken to close this gap. We are aiming at taking advantage of these opportunity and we hope your concept can propel us forward with speed...
I want make a new car self
Permalink
I want make a new car self power generate but I have no economy any bade help me
bros i'm also in the same
Permalink
In reply to I want make a new car self by girish (not verified)
bros i'm also in the same problem. I hav a design but don't know next step. I even fear to share my design. How can I securely produce this?
1. design in CAD
2. find sponser
3. produce
But how ?? where? ?? whom?? I don't know
Thanks so much! I really
Permalink
Thanks so much! I really appreciate it!
i am a engineeg
Permalink
i am a engineeg
How many persons are involved
Permalink
How many persons are involved in designing a car?.
Is the same person who does 2d(hand drawing) sketch , designs the 3d (CAD)?.
Is it compulsary that who does the 2d sketch to do 3d design also?
I have some more doubts can u please clarify it?
my phone number : 8681836120
I'm a mechanical student(first year).